Harnessing API Resources for AutoCAD® and Civil 3D®
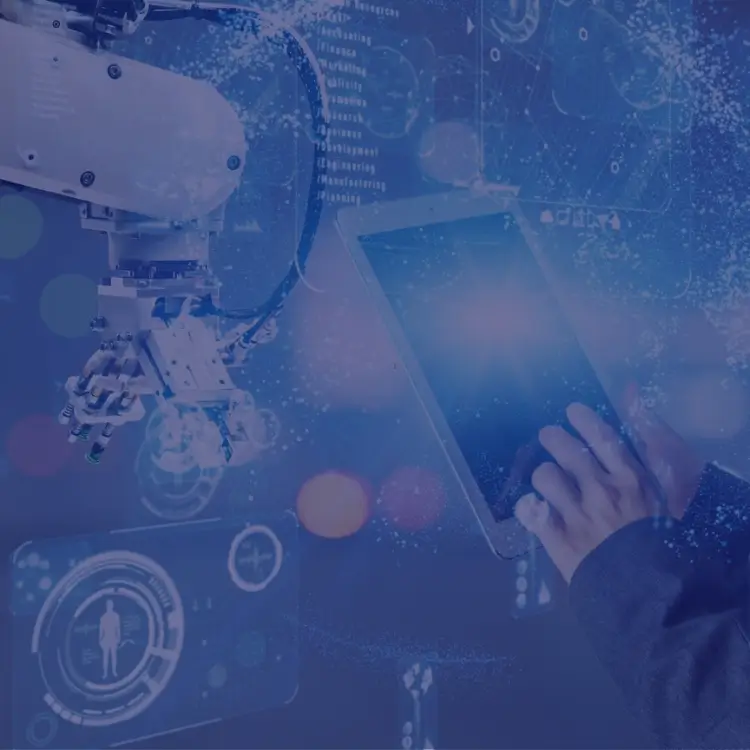
Harnessing API Resources for Autodesk® AutoCAD® and Autodesk® Civil 3D® In the Architecture, Engineering, and Construction (AEC) industry, data accessibility and utilization are paramount. Autodesk® AutoCAD® and Civil 3D® software offer robust Application Programming Interfaces (APIs) that empower professionals to customize workflows, automate tasks, and enhance productivity. Below is an overview of key developer resources specific to these platforms, designed to facilitate data querying and extraction. AutoCAD® Development Resources 1. Development Docs (Start here) Overview: A comprehensive resource providing detailed information on AutoCAD® APIs, including tutorials, guides, and reference materials. Benefits: Serves as the foundational starting point for developers to understand and effectively utilize AutoCAD® APIs. Resource: API Documentation 2. ObjectARX® (C++ API) Overview: A C++ class library that allows deep integration with AutoCAD® software. Benefits: Enables the creation of high-performance applications that can directly interact with AutoCAD®’s internal structures. Resource: Overview of ObjectARX 3. .NET API Overview: Provides managed code access to AutoCAD® functionalities using languages like C# and VB.NET. Benefits: Simplifies the development process with a more accessible programming model. Resource: Managed .NET Developer’s Guide (.NET) 4. AutoLISP® Overview: A domain-specific language designed for automating tasks and customizing AutoCAD® software. Benefits: Ideal for rapid development of routine automation and customization tasks. Resource: Introduction (AutoLISP) 5. ActiveX®/COM API Overview: Allows automation of AutoCAD® software through COM interfaces, suitable for integration with other Windows applications. Benefits: Facilitates interoperability between AutoCAD® and other software, enabling complex workflows. Resource: AutoCAD ActiveX and VBA Reference Civil 3D® Development Resources 1. Developer Docs (Start here) Overview: Provides access to Civil 3D® functionalities through managed code, allowing for customization and automation. Benefits: Enables developers to create applications that interact with Civil 3D® objects and data. Resource: Civil 3D API Overview 2. API Developer’s Guide Overview: Allows for automation and customization of Civil 3D® software using COM interfaces. Benefits: Suitable for integrating Civil 3D® with other applications and automating tasks. Resource: Civil 3D API Reference 3. Dynamo for Civil 3D® Overview: A visual programming tool that integrates with Civil 3D®, enabling users to automate tasks, process complex data, and generate geometry without extensive coding knowledge. Benefits: Empowers users to create custom scripts and workflows, enhancing design efficiency and reducing manual efforts. Resource: Dynamo for Civil 3D Summary Leveraging the development resources available for AutoCAD® and Civil 3D® software can enable you to work with your data in a variety of ways. Whether you’re automating repetitive tasks or developing custom applications, these APIs provide the tools necessary to optimize your workflows. Need assistance with automating and integrating your AutoCAD® and Civil 3D® data? Our expert team is here to help. Contact us today to learn more about our development services tailored to your needs. Trademark Attribution Autodesk, AutoCAD, Civil 3D, ObjectARX, AutoLISP, and ActiveX are registered trademarks or trademarks of Autodesk, Inc., and/or its subsidiaries and/or affiliates in the USA and other countries. 1-800-356-8933 info@ENGworksGlobal.com Facebook Twitter Instagram Youtube Linkedin Back to the Blog Related Posts Elevate Your Workflow – Computer Mouse Devices Elevate Your Workflow – Computer Mouse Devices • August 30, 2022 Visualizing BIM Content Quality and its Impacts Visualizing BIM Content Quality and its Impacts • May 26, 2022 Are You Losing Trust in Fabrication Content? Are You Losing Trust in Fabrication Content? • May 10, 2022
Elevate Your Workflow – Computer Mouse Devices
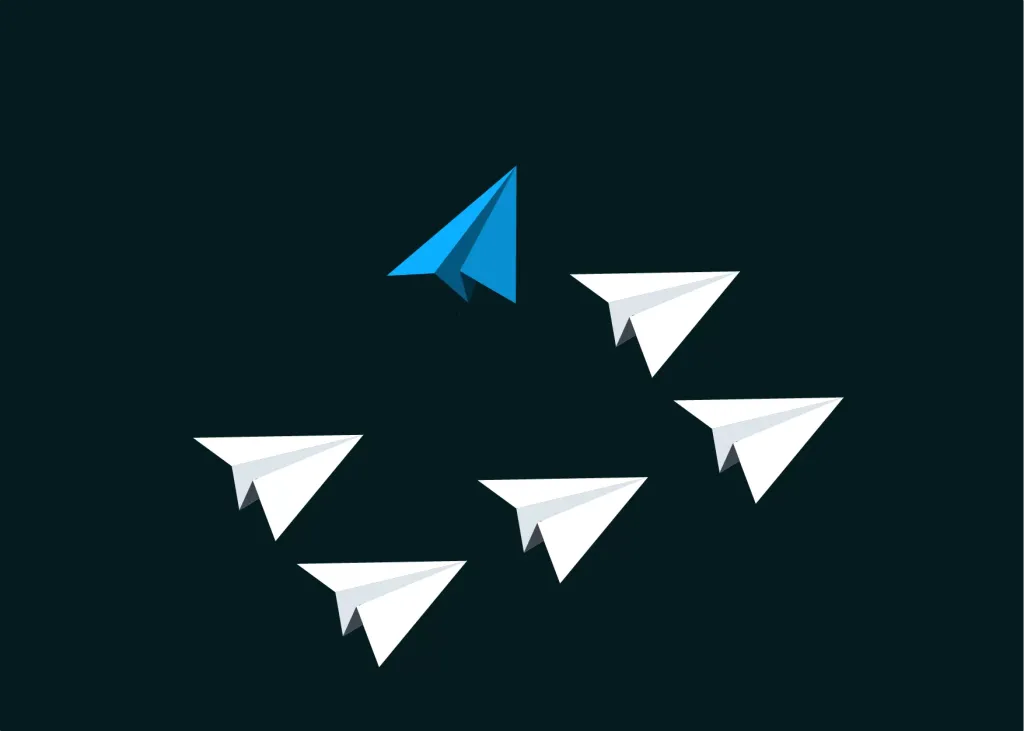
Elevate Your Workflow – Computer Mouse Devices Productivity comes in many forms, whether it is the tools, the technology enabled communication, connected workflows, or even the mindset. The ENGworks Global office recently took a survey called “Elevate Your Workflow” with a theme that focused on computer mouse devices. We participated in this survey because we were curious to know if there was an edge to using particular devices in BIM related roles. Whether it was the lights, the buttons, or cool racing stripes… we wanted to understand what moves the needle in productivity. Most importantly, we wanted to pass those insights on to you. Read further to see our analysis, our survey results, and our top 10 recommendations to elevate your workflow. Highlights from the Survey Responses To start off, here is a visual that shows an overall ranking with the top three features across all mouse devices that appeared in the survey results. Now, let’s get into an analysis of specific features. Programmable Buttons & Wireless vs. Wired Debate In my personal experience, I have found that equipment meant for gaming purposes can work well in CAD and BIM related roles. Gaming equipment has a lot more features, customizations, buttons, and the performance to handle long durations of use, which could be a very suitable solution in the AEC industry as well. Programmable buttons on mouse devices are popular for gaming because of the built-in shortcuts and macros that can be context specific in different games. With the plethora of software available in the industry, I had wondered if that would translate as a use case for shortcut commands in Autodesk® Revit® or AutoCAD®, for example. To my surprise, more programmable buttons didn’t always necessarily mean “better” or “more popular.” In fact, mouse devices with fewer than five buttons received almost double the amount of survey responses compared to those that exceeded 10 buttons. These mouse devices also tripled the amount of responses compared to those that had 6 to 10 buttons. Additionally, the race was very very close between wired and wireless mouse devices. It just so happens in this office that wired beat out wireless mouse devices, according to the number of survey responses. Full Feature Breakdown Here is a full breakdown of all features and all mouse devices that appeared in the survey results. Notice that several differently ‘called out’ features are noted by independent survey respondents and ultimately result in similar mouse recommendations. Mouse Device Recommendations Here are our mouse recommendations along with comments about each one. 1 – Logitech G502 HERO: This mouse device is the most popular device in the office. It is noted that while it is Number One on the list, the 10+ button feature category responses are only attributed to this mouse device and no others. From my personal experience, I have programmed the lower rhombus shaped button as a trigger to make emails automatically read and archived to a certain folder. I have also configured the top scroll wheel to automatically set up an MS Teams invite by toggling it to a hard left. Finally, the lights are pretty cool. Here are additional comments about this mouse below. “Many programmable buttons within easy reach of index finger/thumb.“ “Ergonomic, suitable for palm and claw style grips.“ “Unlike other mice with programmable buttons, this mouse uses the G-Shift button that gives double functionality to each programmable button.“ “Increases speed“ “Programmable buttons that are context specific.“ 2 – Logitech M500: This mouse device is the next most popular mouse device in the office. Based on the comments below, it seems simple yet mighty. For those who are interested in something that just gets the job done and do not need a lot of bells and whistles, check out the comments below. “Simple, easy, responsive…not too complicated“ “It has outlived 3 PCs and hasn’t failed me yet.“ “It allows me to navigate different facets of my work environment more quickly.“ “Reliable“ “Cool racing stripes”*** 3 – Logitech MX Master: This mouse seems to be a step up from a traditional design but with a little ergonomic flair. “Ergonomic design is nice for long work days, and the app specific customization makes me more efficient.“ “Ease of use and comfortable in hand.“ 4 – DELUX Ergonomic: This mouse is definitely for those who are more serious about ergonomic design. Those who experience strain from using traditional mouse devices may benefit from thinking outside the box a bit. “The position of the wrist and hand while using a vertical mouse is more comfortable than twisting the wrist to match the traditional mouse. If you have to pull your hand out every once in a while because it’s strained, then comfort is the most important criteria here.“ “Programmable buttons in the mouse decrease the time of travel from your mouse to keyboard and back to mouse when performing commands, therefore, increasing productivity. The keyboard can also have programmable buttons so this is not that big of a criteria.“ “Vertical Position“ 5 – 3Dconnexion SpaceMouse® Wireless: Well, this is certainly a different design altogether. Rather than a re-purposed gaming mouse, this mouse seems to have been designed specifically for those using CAD applications. “6 degrees of Freedom with 3D modeling software. Aids in easier navigation and makes the 3D model navigation in Navisworks/Revizto look more professional for Coordination meetings.“ 6 – iClever Ergonomic: The picture really doesn’t do this one justice. This one also appears to have more of a vertical design. It gives off a feeling of working on while on the beach with its interesting seashell shape. “Extended wrist rest provides user friendly experience, and avoids any hand pain.“ “Hours of clicking sounds can be annoying. The reduced tip noise improves concentration, learning, and productivity.“ 7 – Razer Naga Hex V2/Trinity: According to the website, “Razer™ is the world’s leading lifestyle brand for gamers.”(MOBA / MMO Gaming Mouse – Razer Naga Trinity). This could be another great option for those interested in mapping keyboard
Visualizing BIM Content Quality and its Impacts
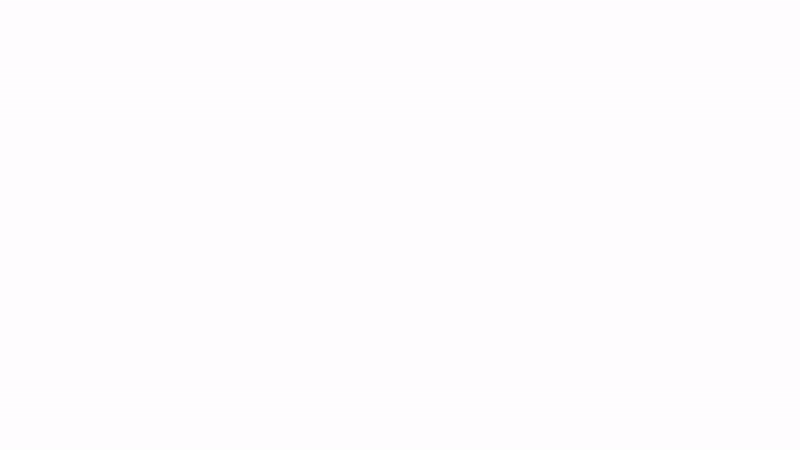
Visualizing BIM Content Quality and its Impacts Safety glasses. Forklifts. Yellow lines. These were common sights I experienced from working for a manufacturer for almost a decade. I often found myself walking through the shop floor to get to meetings. My specific role was in supporting CAD/BIM software platforms for AEC professionals using software such as Autodesk® Revit® and Fabrication CADmep™. I managed manufacturer specific BIM content assets. That said, it was great to have the constant reminder about the realities of the real-life manufactured product in the back of my mind. It proved to be a defining chapter in my career. Valuable Experience – Valuable Benefits It is so valuable to have first-hand experience, especially in an industry where there are labor and skill shortages. In addition to shortages, there are often disconnects between field and office. A couple of years ago, I put out a very informal poll on Twitter. I asked how many times someone as an AEC professional has visited a job site or visited a shop floor. About 20% of the sixty-four votes on that poll stated that they had fewer than ten visits or first-hand experiences. Out of that segmented group, over half stated they had fewer than five visits or first-hand experiences. Note that the informality of the poll did not cover additional details such as career stage, additional breakdowns beyond ten visits, and the trade involved. My purpose for that poll was hoping that the percentage of people visiting job sites or shop floors does not go down over time. This is especially the hope, given that we have experienced a lot more virtual and flexible situations in the industry over the last couple of years. BIM is a technology that can accelerate productivity in the construction industry. If we are to truly realize the full potential, we can focus on BIM content as an incredibly effective driver. To do this, we need to focus on what matters. Focusing on what matters includes integrating real-life constructability and compatibility scenarios. This is especially the case for helping AEC professionals who may experience challenges with resources, training, productivity, and more. Without the right focus, you end up with digital paperweights that unfortunately do not serve the need. On the other side of the coin, trying to make something look perfect in software might not translate to a real-life benefit. BIM Content – More than a Download BIM content (especially for manufacturers) has the potential to be so much more than a download. If we don’t focus on the right things, however, we risk losing the forest for the trees. At a base level, a downloaded file is simply another file in someone’s Downloads folder. It says nothing definitive about what someone did with that download or if it worked for their workflow. Therefore, a downloaded file is not a guarantee that a building product manufacturer product was specified in a project. In addition, a downloaded file could make or break the user experience. For manufacturers interested in making efforts in a BIM content strategy, there is a cost not only in inaction. There is also a cost in acting without both a macro and micro focus on the right things. Taking it further, there is a cost without sustained action. So, to consider BIM content more than a download, we need to change our thinking about it. We propose to define the whole concept of manufacturer BIM content a bit differently. We think of BIM content as a digital asset that represents an actual product in more ways than just appearance. Manufacturer BIM content is a digital asset that represents the product in terms of critical dimensions, clearance, performance, adherence to product standards, availability, applicable features, and system applications. Manufacturer BIM content needs to do this while functioning to the best of its ability in the current releases of the intended software and with respect to the product lifecycle. That is quite a lot of pressure on a downloaded file. How do we address this? The Approach Matters If we are not careful, one-size-fits-all approaches and quick fixes are about as fruitful as the claw games at arcades. I am talking about the ones where you put about $5.00 of quarters in only to leave with a low-quality stuffed animal. Or worse, you end up with nothing for the effort. Additionally, in a real-life piping system, a common phrase I learned from working for a manufacturer is that the system is really only as strong as the weakest point. Connections on fittings are often the weakest point (LeVesque, 2017). In the same way, BIM components, especially those meant to connect to pipe and other elements, are potentially the weakest point in your project. Therefore, quality BIM content for manufacturers needs a more thorough and multi-faceted approach to bridge the gap between real-life product scenarios and digital design for better outcomes. The tricky part is defining quality in a way that is not a blanket statement. Several areas may have potential to have “weak points” or deficiencies with respect to many factors. Different AEC professionals place different levels of importance on various things: Introducing the Quality Polygon Score Defining high quality BIM content risks being too subjective if we do not consider a bigger context as well. To visualize something with a more comprehensive lens, we have created the BIM Content Quality Polygon Score, or QPS for short. The QPS is derived from a series of “Yes”/”No” questions. The questions span in a variety of categories pertaining to Geometry, Functionality, Management, User Experience, and Product Data. In addition, there are sixteen sub-categories. Much like the detailed assessments you can get for your car, the QPS is a seventy-five point assessment we use for evaluating BIM content assets and their likelihood of user utilization. Questions within these categories range from “Can you identify the component as a product in multiple ways?” to “Does this component connect with other components at the right places?” and more. “Yes”
Are You Losing Trust in Fabrication Content?
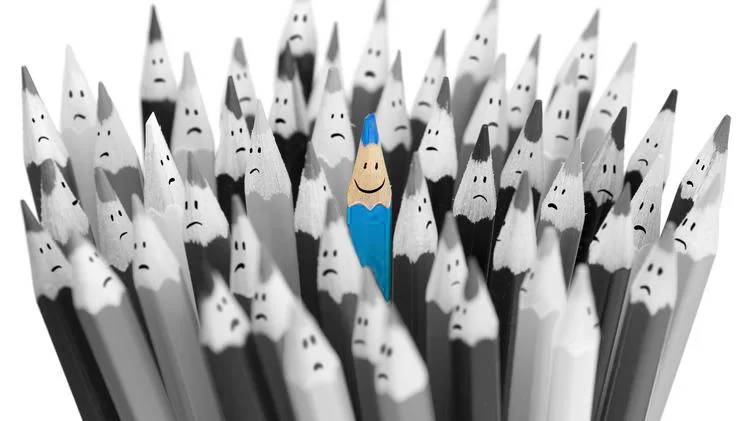
Are You Losing Trust in Fabrication Content? There is an overabundance of Autodesk® Fabrication CADmep™ content as well as numerous resources available for content creation. Unfortunately, the quality content seems to get lost in the shuffle. Incorrect or outdated dimensional data, missing model numbers, redundancies, and more can result in lower quality BIM content for use in Autodesk® Fabrication CADmep™. There are several impacts that contractors face as a result: Significantly increased overall project costs Liability issues Reduced productivity Limited workflows due to lack of software integration With these impacts, it is understandable that a contractor may lose trust in the Fabrication CADmep™ content that is available for download. At ENGworks Global, we believe BIM content can be so much more than a download, and we take quality seriously. Here are the ways we approach quality for the content we create for use in Fabrication CADmep™. What is considered quality content? To qualify as a quality BIM product, Fabrication CADmep™ content needs to be accurate, consistent, and compatible with today’s software needs. Accuracy With the increased use of Fabrication CADmep™ content in the BIM process, accurate content has become a need for modelers, engineers, and professionals. However, we know that is not a simple task because there is a lot of data out there that might have been created for different uses, etc. This creates additional costly challenges. According to an article from Harvard Business Review, knowledge workers waste 50% of their time in “hidden data factories, hunting for data, finding and correcting errors, and searching for confirmatory sources for data they don’t trust.” (Redman, 2017). We actively work in collaboration with various manufacturing teams. In doing so, we can ensure that all data used is certified by the manufacturer and that it originates from the engineering and other manufacturing teams for 100% accuracy. Consistency Consistency is an important aspect of quality across an entire library for a productive workflow. Without consistency, you risk snags and downtime on your projects. Fabrication CADmep™ content is considered consistent if an ITM’s connectivity, naming convention, product CID templates, and other factors are being utilized with best practices consistently. We incorporate product ID, dry weights, model numbers, UPC and HPH codes as the minimum metadata required for our content to meet and exceed end-user expectations. Compatibility Compatibility and functionality are two significant features expected in every fabrication part. A lot of content available in the market today is created with unique connectivity rules. This limits overall compatibility with out-of-the-box content and with content such as pipes and tubes. With the constant innovation and technological advances, all newly built content needs to be compatible with the latest software trends. This allows content to seamlessly fit in with the existing workflows. Our Fabrication team continuously verifies our content to assure full functionality and software integration that suits state-of-the-art BIM processes. Now that we’ve gone over several factors of quality involved with Fabrication CADmep™ content, it’s important to note that these are not individually independent considerations. All of these and more are part of our multi-faceted approach as we serve the industry. Our content is called certified Autodesk® Fabrication CADmep™ content because we know that focusing on the right things not just once but over time creates better outcomes. Leveraging manufacturer certified content provides an enhanced user experience with the following features: Correct and applicable representation of parts Correct connections Correct installation capabilities Correct metadata needed for purchasing and estimate reports Certified content provides significant benefits for design teams: Accurate bill of materials (BOM) Accurate installation drawings Accurate coordination with reduced field issues Accelerated time to production, installation, and beyond Next Steps The complicated nature of Autodesk® Fabrication CADmep™ content and the challenges associated with creating, managing, and updating it creates a gap that is tedious, risky, and expensive to bridge alone. ENGworks Global offers an all-encompassing service that involves all the necessary steps to provide your team with highly efficient quality content. Letting us handle your content needs with our expertise will provide more time for your team to focus on modeling, estimation, and project management. We have over 15 years of experience in content creation along with an outstanding industry reputation. We pledge to provide unlocked quality with certified Fabrication CADmep™ content for better outcomes on your projects. To learn more about our content creation, fabrication, and administration services, contact us at info@ENGworksGlobal.com Sources Cited: Redman, T. C. (2017, October 4). Bad Data costs the U.S. $3 trillion per year. Harvard Business Review. Retrieved May 26, 2022, from https://hbr.org/2016/09/bad-data-costs-the-u-s-3-trillion-per-year Autodesk Trademark Notice: Autodesk, the Autodesk logo, Revit, and Fabrication CADmep are registered trademarks or trademarks of Autodesk, Inc., and/or its subsidiaries and/or affiliates in the USA and/or other countries. This publication is independent of Autodesk, Inc., and is not authorized by, endorsed by, sponsored by, affiliated with, or otherwise approved by Autodesk, Inc. The ENGworks Global Team Please also connect with us on our social media platforms below to stay up to date with our announcements. 1-800-356-8933 info@ENGworksGlobal.com Facebook Twitter Instagram Youtube Linkedin Back to the Blog Related Posts Elevate Your Workflow – Computer Mouse Devices Elevate Your Workflow – Computer Mouse Devices • August 30, 2022 Visualizing BIM Content Quality and its Impacts Visualizing BIM Content Quality and its Impacts • May 26, 2022 The 2022 AEC Integration Summit Recap: All Aboard the Train to Connect People and Data The 2022 AEC Integration Summit Recap: All Aboard the Train to Connect People and Data • March 2, 2022
The 2022 AEC Integration Summit Recap: All Aboard the Train to Connect People and Data
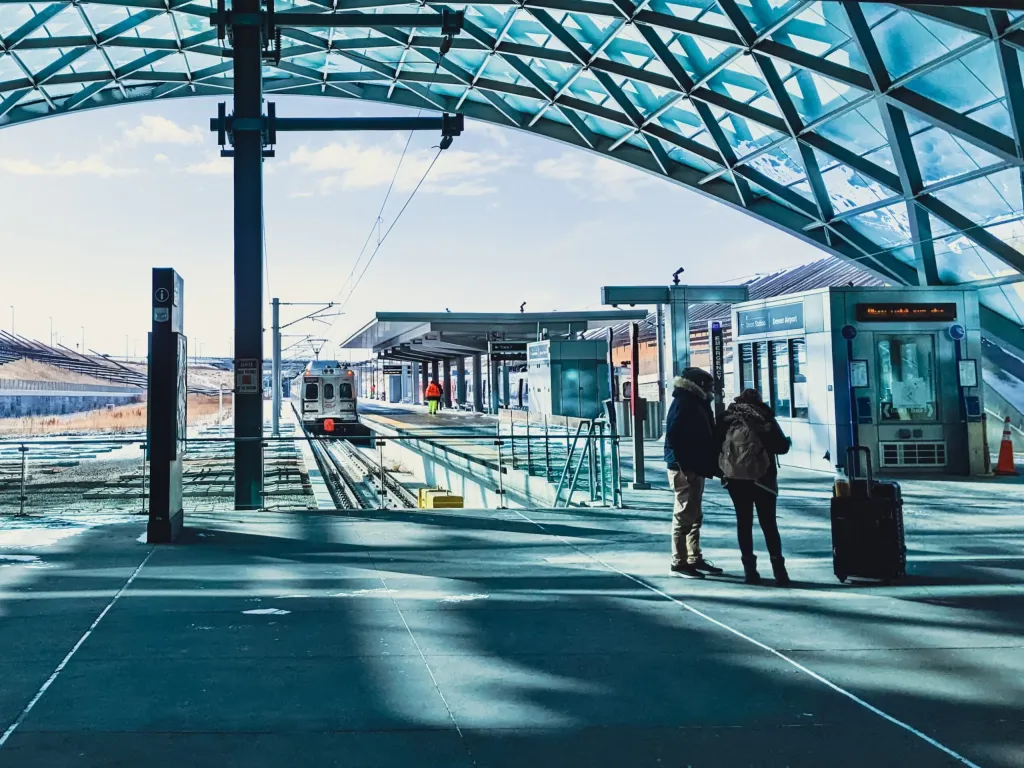
The 2022 AEC Integration Summit Recap: All Aboard the Train to Connect People and Data Ding Ding. A bell chimes as the train leaves the station at the Denver, Colorado International Airport to make its way to Union Station. Some travelers are weary, and some are energized for the adventure that awaits. Meanwhile, train personnel walk up and down the train to ensure all have a ticket with the correct information on it. Whether those travelers leave the train at one stop or another, or they board another train with a transfer, the train ticket is paramount to get to where you want to go. In my case, my destination was the Construction Progress Coalition 2022 AEC Integration Summit that took place at the Hotel Kimpton Born, just a few steps away from Union Station. Like the train transportation system, the building asset supply chain in a construction project can appear on the surface to function in a comparable way. However, it is not that simple in practice, as I have explored further while participating in the Summit as a primary stakeholder, representing the building product manufacturer (BPM) for the MEP component team. Coming from a background of working for a building product manufacturer for almost a decade, I grew very much accustomed to not just processes but dealing with complexity, or as I like to say, “rolling with the punches.” I worked at the intersection of many distinct groups to support the real-life product as it existed in various software platforms for design purposes such as successful BIM implementation. BIM content itself is a digital asset, and quality matters with the help of supported processes in a supply chain. I learned so much from everyone I interacted with and found immense joy in making connections from various places. The ”train ticket” for me was (and still is) in the data. Visuals Enter the Common Data Exchange (or CDX, for short). According to the Construction Progress Coalition’s website, the “Common Data Exchange (CDX) is a framework for project stakeholders to communicate interoperability rules and requirements between two or more parties. CDX is not a standard, per se, but a visual representation of workflow and data exchange requirements between supply chain parties.” (Wood, Common Data Exchange (CDX)). Here is what I love about the Common Data Exchange concept. The fact that it is more focused on visual representation of a workflow is so refreshing. I have been a huge fan of mind maps, concept maps, and other forms of visual thinking for years. I even wrote an article about my experience in using visual mind maps in the November 2020 issue of AUGIWORLD magazine. The flexibility in displaying information in a more open way for different situations allows me to focus more on conveying ideas than on how to format them. It also helps us get away from the “we’ve always done it this way” trap if a certain situation calls for something different. That does not mean there is not a form of a structure though. The CDX framework used at the 2022 AEC Integration Summit included magnets and stickers with specific symbols representing documents, databases, current state, future state, connections, people doing certain activities, and more. Everything down to the actual sticky note color had a reason and meaning. The framework was there in visual symbols, but the actual idea conveying activities was flexible because all team stakeholders could move things around, write in words, and add lines and connections wherever it made sense on a large whiteboard. This proved to be extremely helpful because what is interesting between manufacturing and construction is that sometimes the same words can mean very different things to people in different roles. In an industry where there are so many buzz words and acronyms, any sort of clarity on what we are talking about would be greatly helpful! Linguistics This brings me to the next thing I enjoyed about collaborating with the team at the Summit. The facilitation of such an event really made us question everything down to the actual words we were using in the problem statement and what we were hoping for in the outcome. Yes, we even broke out the thesaurus and dictionary on a few occasions! The objective for the MEP component team looks like this, but I can tell you after working with the group that it does not necessarily mean that words are set in stone. Word choices really do matter and solving the most complex problems comes with asking the right questions in the first place. Perspectives People may say that they enjoyed an event, a group, or otherwise because of the “like-minded” individuals. I think, in this case, the only “like-minded” part is in a common goal to improve things across the entire industry. This event was full of different perspectives that can result in perceptions being different from intentions and contextual realities that are different but valid. A great visual often used in Systems Thinking is the story of “The Blind Men and the Elephant.” Essentially, the story goes on to describe how each person approached a different part of the elephant and concluded something different about it. This story illustrates those individual perceptions, while true and valid for that individual, can lead to miscommunication and conflict if we are not careful because it is not the full context (Saxe, 2015). Participating in the 2022 AEC Integration Summit gave us an opportunity to explore the context of our MEP System Component “elephant.” Put in another way, the summit allowed us to put the strengths of generalists and specialists to work. Naturally, the book “Range,” by David Epstein validated my experience in deliberately choosing to be more of a generalist and a connector in a world where specialization and depth in one specific domain are favorable (Epstein, 2019). However, when we are not careful, silos of data develop, duplicate and manual efforts take place, and trust is low. The thing is, I think
Utilizing BIM to Improve Modular Construction Workflows
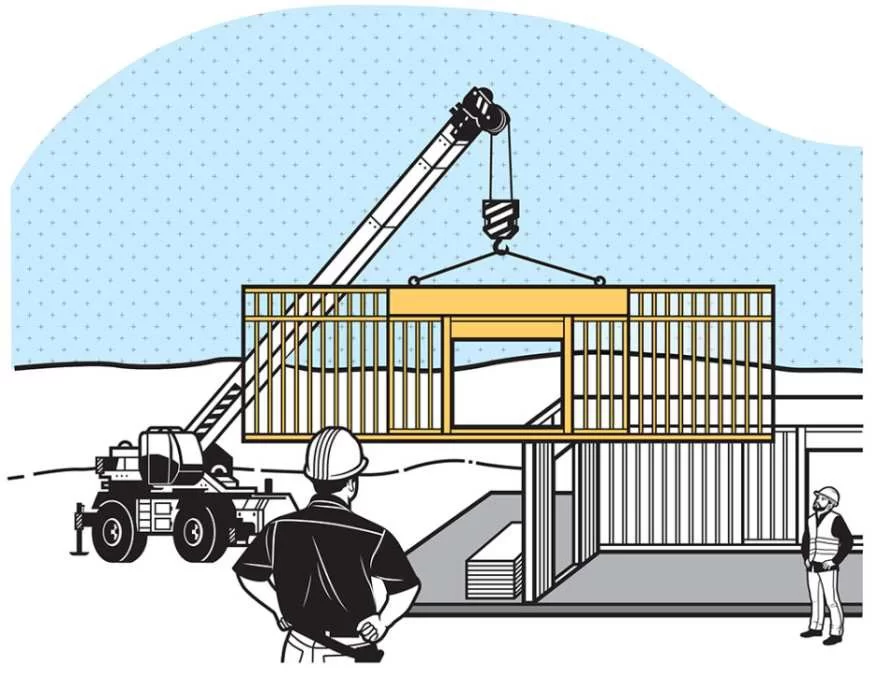
Utilizing BIM to Improve Modular Construction Workflows Modular construction has become increasingly popular in recent times. A lot of it has to do with improvements in industry technology and workforce skills. Adopting ideas from other industries and introducing Project Management techniques to deliver a more efficient outcome is driving construction professionals to ask; How can we improve this? at every step of the way. In the recent panel discussion “Furthering the Use of Modular Construction Using BIM” from The Festival of BIM & Digital Construction, Amy Marks, Head of Industrialized Construction Strategy & Evangelism at Autodesk Construction Solutions, also the moderator of the panel discussion, described the current megatrends in the construction industry as follows: Big Data & Analytics, Robotics & Automation, Prefabrication, IoT, and Additive Manufacturing. The panel discussion on furthering the use of modular construction using BIM covered a lot of key elements regarding the rising reliance of the modular industry on BIM. Amy compared BIM to the Autobahn (a federally controlled-access highway system known for its lack of a mandated speed limit) and all our workflows/techniques as the cars that drive on the Autobahn. The introduction also sheds light on the Prefabrication Continuum. Prefabrication Continuum is a broad term that encompasses the creation of building elements in a controlled environment that are transported to their final destination preferably installed on-site using accelerated assembly methods. Advanced Building Products: These include products that reduce drying time, curing time, welding efficiency, and waiting time. These products are often part of the specifications and result in improving process efficiency. Single Trade Assembly: As the name suggests, these products are focused on a single trade. Pipe spools and light gauge wall panels are instances of single trade assembly. Often, subcontractors are the responsible party for these assemblies. Multi-Trade Assembly: Multi-trade assembly involves multiple trades as a part of their assembly. Bathroom pod is one such example for a Multi-trade assembly. Volumetric Module: Volumetric modules are modules that build a modular structure. If applicable, it will include elements from all of the above. During the panel discussion, there were two polls taken from the audience regarding the prefabrication continuum, the first poll question was the current relative use of assembly methods mentioned in the prefabrication continuum and the second poll question was the future use of the different assembly methods. The audiences posted an even score for all methods in the first poll, however, the volumetric modules got the most votes for the second poll. The polls highlighted how the industry professionals have put their interests and faith in the rising popularity of the volumetric modules. Design for Manufacturing & Assembly (DfMA) DfMA is a design methodology to enable and optimize prefabrication through a set of design choices (principles). It comprises of Design for Manufacturing (DFM) and Design for Assembly (DFA). An example of a panel installer was discussed, who would abide by a set of instructions for the designer to follow. There were incentives in form of discounts that would be offered for the designer if they would include a certain number of minimum set of instructions from the panel installer. The instructions were laid out such that it would make the panel assembly more effective to install. Disassembly & Reuse (DfMA–DR ) It is defined as a design methodology to enable and optimize prefabrication aligned with the circular economy. It means that the methodology promotes reusing and technological swaps between different assemblies as shown in the image below: The panel discussion was very insightful and touched upon a lot of interesting topics mentioned above such as Prefabrication Continuum, industry mega trends, and DfMA that are beneficial to the industry personnel interested in adopting BIM for modular construction. The Q&A session covered a few interesting topics as well like the panel member’s advice to the newcomers to the BIM Modular world. Steven Eglinton (Global Tutor & Speaker, Director of BIMEnable & GeoEnable, Principal Tutor in BIM, Institution of Civil Engineers), suggested the focus to be on overall purpose, high-level processes, and process improvements. Steven talks about how technology has improved and now there is a dire need for education in adopting the technology. Ian Peter Atkins, BIM Manager at Populous, urged the newcomers to engage with curiosity and efficient communication. Bridget Proulx, BIM Manager at Kitchell Contractors, called the importance of having efficient translators between different teams. Julide Bozoglu, Design and Construction Technologist at Illinois Institute of Technology, with her experience in the academia and industry, understands the importance of cross-functional teams in achieving efficient results. Amy urges the newcomer to get on the cloud and adopt BIM in their workflows as soon as they can. She believes that process, culture, and leadership can enable teams to meet all prefabrication goals. Despite playing different roles in their day to day lives, the panel collectively believes that the Designers and General Contractors both should understand each other’s roles better in addition to understanding their own roles. This will generate a better understanding of the overall process, help in identifying bottlenecks in the process, and achieve effective collaboration to resolve and predict issues. ENGworks’ goal to push BIM workflows matches the need for integrated modular teams. ENGworks can help clients design, model, and coordinate volumetric modules that meet predetermined standards thereby delivering a design that improves the construction processes. Contact us today to help you get started with your next project. Please also connect with us on our social media platforms below to stay up to date with our announcements. 1-800-356-8933 info@ENGworksGlobal.com Facebook Twitter Instagram Youtube Linkedin Back to the Blog Related Posts Elevate Your Workflow – Computer Mouse Devices Elevate Your Workflow – Computer Mouse Devices • August 30, 2022 Visualizing BIM Content Quality and its Impacts Visualizing BIM Content Quality and its Impacts • May 26, 2022 Are You Losing Trust in Fabrication Content? Are You Losing Trust in Fabrication Content? • May 10, 2022
ENGworks Webinar Review: Managing BIM Coordination Workflows with Revizto
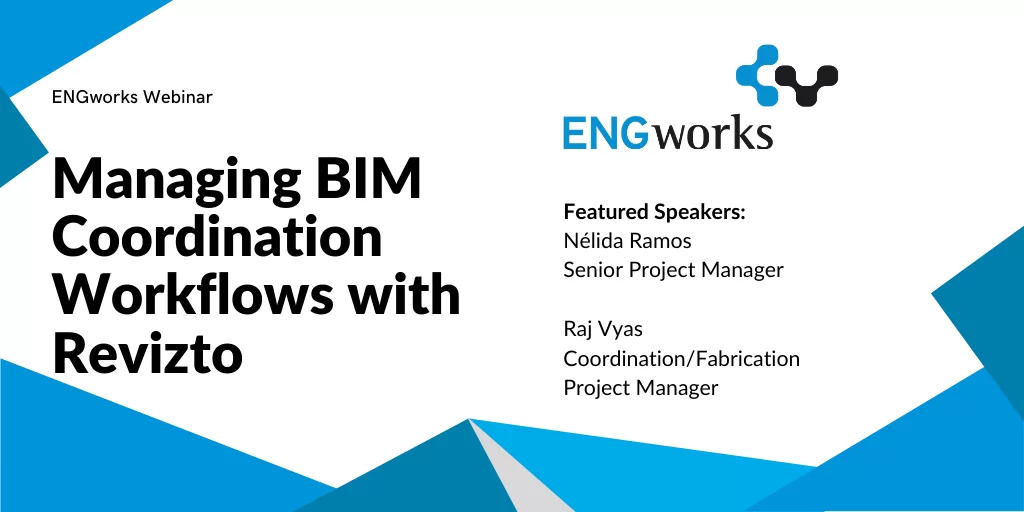
ENGworks Webinar Review: Managing BIM Coordination Workflows with Revizto With the influx of software in the construction industry, it is becoming increasingly difficult to find one software that meets all the needs of the ever-growing industry. Performing a successful BIM coordination requires a well-tracked clash detection, organization, discipline, consistency, MEP knowledge, and good software to help you deliver all this in one place. Here at ENGworks we have worked with a lot of BIM coordination projects where we had the opportunity to implement Revizto software in different phases of the project’s lifecycle. What is Revizto? Revizto is a real-time issue tracking software for Architecture, Engineering, and Construction with a focus on collaboration and BIM project coordination. It unifies BIM intelligence and makes it immediately accessible and actionable for the entire project team. With Revizto’s advanced Issue Tracker, project team members can identify and manage model-based issues in the 3D space and on 2D sheets, including addressing clash groups from Navisworks. Additionally, Revizto allows users to follow progress or resolve challenges in real-time all while on any device and in VR. Our success at ENGworks with Revizto has been through the Design, Pre-Construction, and Construction phases of the projects. Using Revizto not only helps with the clash detection and issue tracking, but it also helps with the communication between the design, construction, and operations stakeholders. Some additional topics and demos you can find in this webinar: BIM Coordination Workflows Revizto Workflows Export 2D Sheets How to use Revizto for Clash Syncing and Issue Creation Revizto Clash Creation from Navisworks Clash Id Clash Tags Revizto Issue Multi-Edit Functions Clash Reports Dashboards Cloud-Based Platforms Additional Revizto Benefits: Training: There is a lot of training material available online. Revizto has its own training library. Learning Curve: Easy learning curve with the software. Support Team: Fast response time from Revizto’s support team. New Features: Regular addition of new features. As promised, here’s the link to the live webinar recording. We’re sorry for those who couldn’t make it, but we think you can still find it interesting and can watch the recording on your own time. Revizto Library Revizto has a virtual library with its own training and webinars that can help you with your Revizto learning curve. We have collected various of those videos related to our webinar topic that we suggest you watch. Revizto Navisworks Clash Detection Reports & Dashboards Overview Revizto Webinar: Leveraging Revizto During Projects Coordination Revizto Webinar: Get the most our of Revizto Reporting How Can We Help? ENGworks’ team has extensive experience performing BIM Coordination for different projects and applying the Revizto software to enhance the process and communication between the team. We have seen during the years how Revizto has been improving its software for its users’ needs, always staying up to date with the new technology. We are certain about the future of BIM, and we will remain at the forefront of that change. We will continue assisting our clients and colleagues to achieve better workflows and faster turnaround times by adopting the latest technologies and efficient workflow practices. To learn more about our BIM Coordination services, please visit the following links: BIM Coordination Services Design Assist Building Conflict Reporting / Clash Detection BIM for Prefabrication and Fabrication Please also connect with us on our social media platforms below to stay up to date with our announcements. 1-800-356-8933 info@ENGworksGlobal.com Facebook Twitter Instagram Youtube Linkedin Back to the Blog Related Posts Elevate Your Workflow – Computer Mouse Devices Elevate Your Workflow – Computer Mouse Devices • August 30, 2022 Visualizing BIM Content Quality and its Impacts Visualizing BIM Content Quality and its Impacts • May 26, 2022 Are You Losing Trust in Fabrication Content? Are You Losing Trust in Fabrication Content? • May 10, 2022
BuiltWorlds Insights reveals The Adoption Leaders 50 List 2018 and guess who is in it?
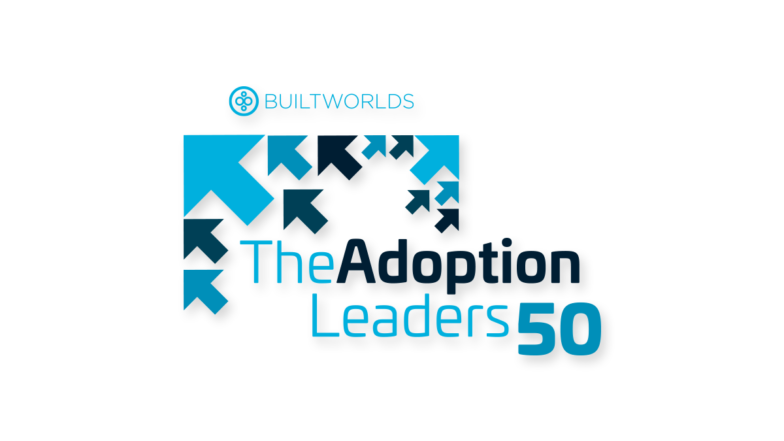
Here at ENGworks, we are happy to announce that our Vice President of Technology and Innovation, Ian McGaw, has been selected by the awesome people of BuiltWorlds in their Adoption Leaders 50 List for 2018. According to BuiltWorlds, all the individuals selected on this list are not only champions of technology of their organizations but leaders who stepped into newly created roles that exist today as the result of increased tech adoption. Want to know more about Ian McGaw? Check out number 29 on the Adoption Leaders List in the link below! You can also find more information about ENGworks on BuiltWorlds directory. https://builtworlds.com/insights/adoption-leaders-50-list-2018/